[accessed 8 Nov, 2021]](./images/Compact-tension-sample-geometry-used-for-fracture-toughness-measurement.png)
The value of $K$ that causes the notch to grow and cause fractures.
This is value is known as the fracture toughness, $K_c$.
At low thicknesses fracture toughness depends on thickness but as thickness increases, $K_c$
decreases to the constant value, the plane strain fracture toughness, $K_{1c}$.
# Composites
Composites are made of two or more materials, which when combined together, at up to a milimetre
scale, have superior properties to their parent materials.
Composites tend to be 2-phase: a dispersed phase in a matrix.
The disepersed phase tends to be fibres (large aspect ratio) or particles (low aspect ratio) which
are embedded in a matrix, which are often resins.
Composite properites are affected by the dispersed phase geometry:
- Shape
- Size
- Distribution
- Relative orientation (for fibres)
## Rule of Mixtures
$E_c$ lies between the arithmetic mean (upper limit):
$$V_mE_m + E_pV_p$$
and the geometric mean (lower limit):
$$\frac{V_mE_mE_pV_p}{V_mE_m + E_pV_p}$$
Where $E_c$, $E_m$, $E_p$ are the Young's moduluses of the composite, matrix, and particles,
respectively, and $V_m$ and $V_p$ are the volume of the matrix and particles, respectively.
## Particle Reinforced Composites
### Applications of Composites
#### Tungsten Carbide Cobalt for Cutting Tools
The Tungest Carbide (WC) particle are a truly brittle ceramic.
They are very hard but the brittleness means they are easy to break.
The solution is to hold small WC particles in a ducitle metal matrix.
In this case it is Cobalt (Co).
This way, crack in one WC particle does not necessarily mean other particles are broken,
meaning the cutting tool overall still works.
Another advantage of this composite is that WC is not very thermally conductive and has a high
melting point, which allows it to work well the environment it's in.
#### Resin Bonded Alumina for Sanding Disks
This is another example of brittle but hard ceramics being put in a ductile matrix.
In this case it's a resin.
It follows the same idea---separating the ceramics into small particles means the particles can
break and the product still works overall, as there are thousands of particles which are not broken.
## Fibre Reinforced Composites
### Specific Property
Specific Property of a composite is a property divided by density of composite.
Here are some examples of specific properties:
- Specific ultimate tensile stress $= \frac{\sigma_{UTS}}{\rho_c}$
- Specific Young's modulus/stiffness $= \frac{E_c}{\rho_c}$
### Influence of the Fibres
Depends on:
- Fibre type
- Fibre length and diameter
- Fibre orientation
- Strength of bond between fibre and matrix
### Stress Strain Graph of a Fibre Reinforced Composite
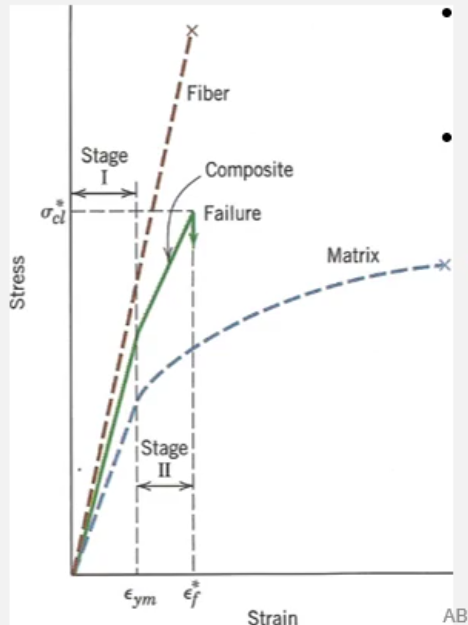
Note that the composite fails at the same strain as the fibres but yields at the same strain as
the polymer matrix.
The elastic behaviour of the composite before yielding is dependent on the strength of the chemical
bonds between the surface of the fibre and matrix.
### Mechanical Performance of a Fibre Reinforced Composite
- Stress/strain behaviour of fibre
- Stress/strain behaviour of matrix
- Fibre volume fraction
- Applied stress direction
Longitudinal is along direction of fibres, transverse is 90\textdegree to direction.
Fibre composites tend to be much much weaker in transverse direction:
Composite | Longitudinal UTS | Transverse UTS
------------ | ---------------- | --------------
GF/PET | 700 | 20
CF/Epoxy | 1000 | 35
Kevlar/Epoxy | 1200 | 20
(All units in MPa)
# Thermal Properties of Materials
## Specific Heat Capacity
How much heat energy is required to raise the temperature of a body by one unit:
$$ C_p = \frac{\Delta E}{m\Delta T} $$
where $c$ is specific heat capacity.
It is measured at a constant pressure, usually $1.013\times 10^5$ Pa.
## Molar Heat Capacity
$$C_pm = \frac{\Delta E}{n\Delta T}$$
#### What is a mole?
> The mole (symbol: mol) is the base unit of amount of substance in the International System of
> Units (SI).
> It is defined as exactly $6.02214076\times 10^{23}$ elementary entities ("particles")
~ [Wikipedia: Mole (unit)](https://en.wikipedia.org/wiki/Mole_(unit))
#### How Much Does a mol of Something weigh?
A mol of an element weighs its relative atomic mass ($A_r$) but in grams.
For example, Carbon-12 has an $A_r$ of 12 (as it's made of 6 neutrons, 6 protons, and 6 electrons
which have negligible mass) so a mol of Carbon-12 has a mass of 12 g.
## Thermal Expansion
### Origin of Thermal Expansion
All atomic bonds vibrate, on the magnitude of gigahertz.
The bonds vibrate about a mean positoin and the vibration is a simple harmonic motion.
From the graph below you can see that as energy (in the form of heat) is supplied to the bonds,
the amplitude of the vibrations get larger and larger.
You can also see the mean position of the bond gets further and further away, meaning the volume
of the material also is increasing.
The mean position of the bond is what dictates the volume, as this means the inter-atomic
separation increases.
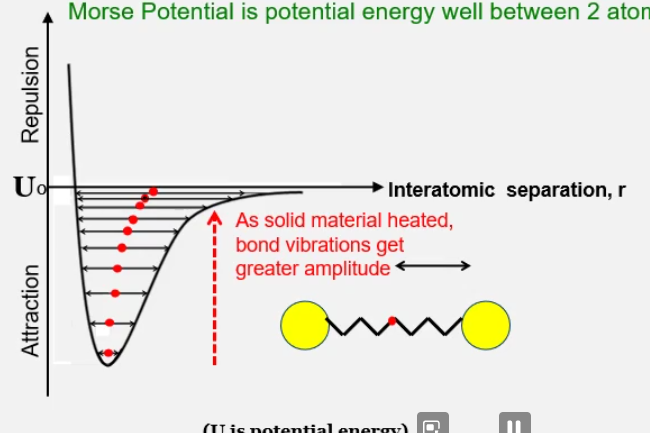
Morse potential is the energy well between 2 bonded atoms.
The graph is asymmetric due to the repulsion experienced by atoms as they apporach.
### Linear Coefficient of Thermal Expansion
$$\alpha_L = \frac{\Delta L}{L_0 \Delta T}$$
where $L$ is the sample length.
#### Example 1
A 1 m long bar of aluminium metal cools in the solid state from 660 \textdegree{}C to
25 \textdegree{}C.
Calculate the length of the bar after it cools down, given $\alpha_L = 25\times10^{-6}$ K$^{-1}$.
\begin{align*}
l_0 &= 1 \\
\Delta T &= T_f - T_0 = 25 - 660 = -635 \\
\\
\alpha_L &= \frac{l_f - l_0}{l_0 \Delta T} \\
\alpha_L l_0 \Delta T &= l_f - l_0 \\
l_f &= \alpha_L l_0 \Delta T + l_0 = 0.984
\end{align*}
### Linear Thermal Expansion and Isotropism
Since isotropic solids have the same properties in all directions, you can say that for an
isotropic solid:
$$\alpha_V = 3\alpha_L = \frac{\Delta V}{V_0 \Delta T}$$
### Reasons to Care About Thermal Expansion
- A coating on a material may fail if the thermal expansion coefficients do not match
- A brittle material may thermally shock and fracture due to thermal expansion mismatch between
the ouside and inside, especially if the material is not very thermally conductive
## Thermal Conductivity
Thermal conductivity is the rate at which heat power is transferred through a material.
$$\frac{Q}{A} = k \frac{\Delta T}{\Delta x}$$
where $Q$ is heat power, $A$ is area of the surface, $\frac{\Delta T}{\Delta x}$ is the
temperature gradient, and $k$ is the thermal conductivity constant.
### Origin of Thermal Conductivity
Heat is transferred through materials by electrons (and partially by atomic vibrations)
Metals have high thermal conductivity as their delocalised 'sea' electrons are about to move about
easily.
This makes them excellent conductors of heat and electricity.
Ceramics, glasses, and polymers do not have delocalised electrons and are therefore poor conductors
of heat and electricity (they are insulators).
Polymer foams are even better insulators because they have holes which lowers their density.
# Chemical Bonding of Materials
Chemical bonds are what holds a material together in solid state.
There are 5 main types of bonds:
Type | Dissociation energy
-------- | -------------------
Ionic | 600 to 1500
Covalent | 300 to 1200
Metallic | 100 to 800
Hydrogen | 4 to 23
vdw | 0.4 to 4
The dissociation energy is the energy required to break the bond, or the strength of the bond.
## Materials and their Properties and Bonding
### Ceramics and Glasses
Ceramics and glasses are composed of mixed ionic and covalent bonding.
Their strong and rigid bonds have no ability to slide past each other.
This makes the materials brittle.
### Metals
Metals are based on metallic bonding (woah).
This type of bonding *does* allow for ions to slide past each other, making metals ductile.
### Polymers
Polymer chains made of C-C covalent bonds are strong, like those found in ceramics.
However, in thermoplastics polymers, the materials can yield by having the chains untangle and
then align, as the chains slide past each other.
This means that **stronger bonds between polymer chains means a higher yield stress in thermoplastic
polymers**.
# Crystallisation of Materials
## Atomic Arrangement
- No order
- Short range order
Silica glasses have short range order on the atomic scale.
They are composed of regular SiO$_4$ units which all have the same bond length and bond angles.
However, these units bond together irregularly, which results in different length chemical bonds
and angles between the units, meaning they do not have any long range order.
- Long range order
## Cubic Unit Cells
- Lattice Parameter --- One side of a unit cell
The lattice parameter can be different for each side of a cell.
- Simple cubic unit (SC):
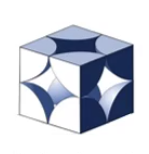
Lattice Parameter = 2r
- Face centred cubic (FCC)
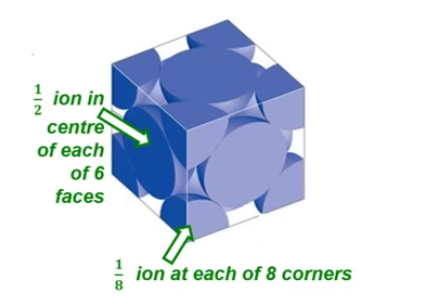
- Body centred cubic (BCC)
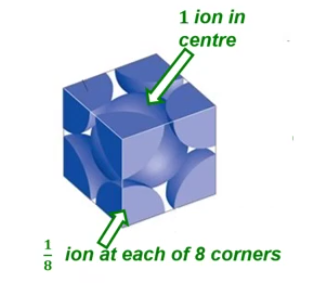
### Packing Factor
$$\text{packing factor} = \frac{\text{ions per unit cell} \times V_{ion}}{V_{cell}}$$
### Theoretical Density
$$\text{theoretical density} = \frac{\text{ions per unit cell} \times m_{ion}}{V_{cell}}$$
### Polymorphism
Example of a polymorphic solid-state phase transfomration of iron at 1185 K and 1 atm:
$$\text{Fe}_{\text{BCC}} \longleftrightarrow \text{Fe}_{\text{FCC}}$$
Below 1185 K and at 1 atm, only BCC exists. Above 1185 K and at 1 atm, only FCC exists.
### Points, Directions, Planes in a Cubic Unit Cell
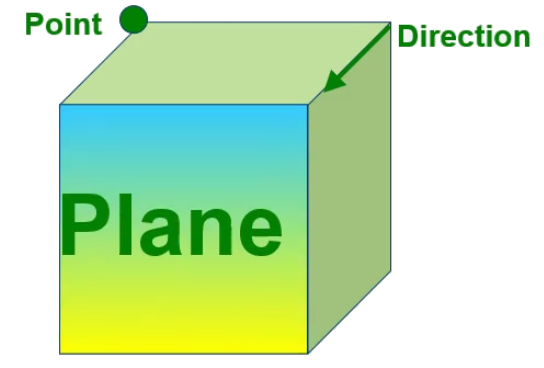
### Slip Systems in Metals
Metal ions lying in close-packed planes and directions move more easily, increasing ductility.
The combination of a close packed plane and direction is called a *slip system*.
A close packed direction is where ions touch all the way along the direction.
A close packed plane is where ions touch all the way on a plane.
FCC metal ductility is mainly controlled by the *(111) slip plane*
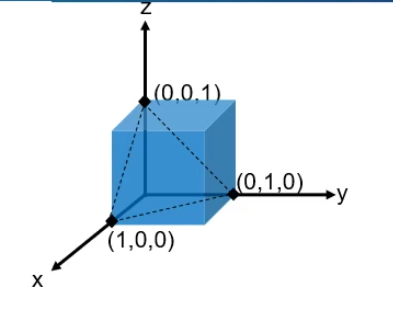
## X-Ray Diffraction (Bragg's Law)
The wavelength of x-rays, $\lambda$, is roughly equal to the distance, $d$, between atom/ion layers.
This allows x-rays to probe for $d$ via Bragg's Equation:
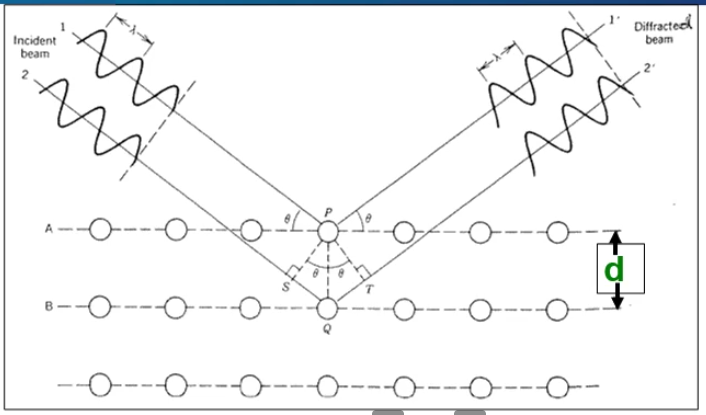
Requirements for the x-rays:
- Monochromatic
- Coherent (phase difference of $2\pi n$ where n is any integer)
- Parallel with each other
The incoming x-rays 1 and 2 strike the rows of ions in the crystal and are diffracted, which can be
considered reflection at the atomic level.
The angle of incidence equals the angle of reflection.
The outgoing x-rays 1 and 2 are coherent only if the extra path travelled by ray 2, $2d\sin\theta$
is any multiple, $n$, of $\lambda$. Or:
$$n\lambda = 2d\sin\theta$$
This is Bragg's Law.
# Metals
## Defects on the Atomic Scale
Defects on the atomic scale have a significant effect on yield stress, ultimate tensile stress, and
ultimate fracture stress.
The yield stress of a real metal(-alloy) is much lower than the theoretical yield stress for
the perfect metal(-alloy) crystal.
This difference is because of the defects in the metal, particularly dislocations, as the
dislocations allow the ions to slide past each other at much lower yield stresses.
The 5 types of defects are:
- Grain boundaries
- Vacancies (missing ion)
- Dislocations (missing row of ions)
- Impurity ions
- Crystalline includison
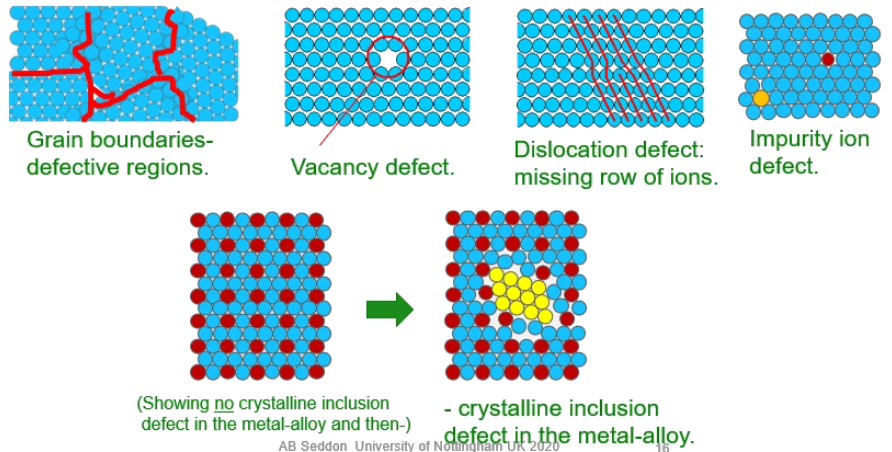
### Dislocation Movement vs. Simple Sliding
The layers of ions in a crystalline metal could simply over each other:
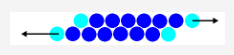
However, the stress required for simple sliding is much higher than the stress required to move a
dislocation.
This is because dislocation motion is successive sliding of the partial plane of ions under applied
shear stress (black arrow).
The vacancy in the slip plane (yellow arrow) moves in steps in sequence from left to right.
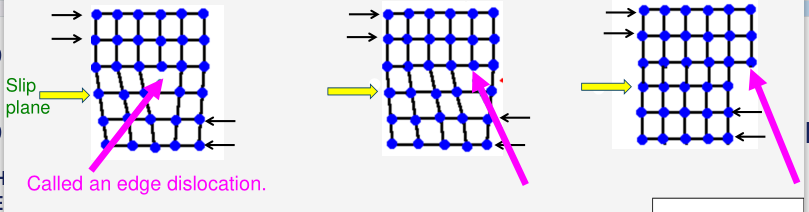
If there are no dislocations then plastic deformation is delayed to a higher applied stress,
meaning the yield stress of the metal would be much higher.
Dislocations move more easily on specific planes and in specific directions called the
slip planes and slip directions which make up what is known as the
[slip system](#slip-systems-in-metals).
There are a very large amount of dislocations in metals and alloys.
Dislocation density is expressed as total length of dislocations per unit volume.
## Single Crystal Metals
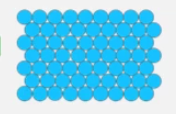
Normally when a molten metal is cooled to a solid, then lots of tiny crystals (grains) grow in
different directions until they impinge.
The grain boundaries are a source of mechanical weakness.
A single crystal metal is one for which the casting is cooled to form just one giant crystal:
1. The molten metal is cast into a mould
2. At the very base of the mould, the temperature is dropped and the alloy crystallises into many
little crystals
3. The crystals grow upwars through the liquid and meet a spiral tube and are constricted
4. This tube only allows one crystal to grow through the spiral and then into the main mould
## Polycrystalline Metals
Most normal metals you see everyday are polycrystalline.
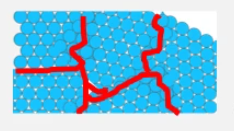

## Elastic and Plastic Strain in Metals
When you apply a tensile stress to a mteal, this will produce a shear stress in any part of the
metallic lattice that is not parallel or perpendicular to the applied stress.
Under the action of shear stress, the metallic lattice will tend to experience a combination of
elastic strain and plastic strain:
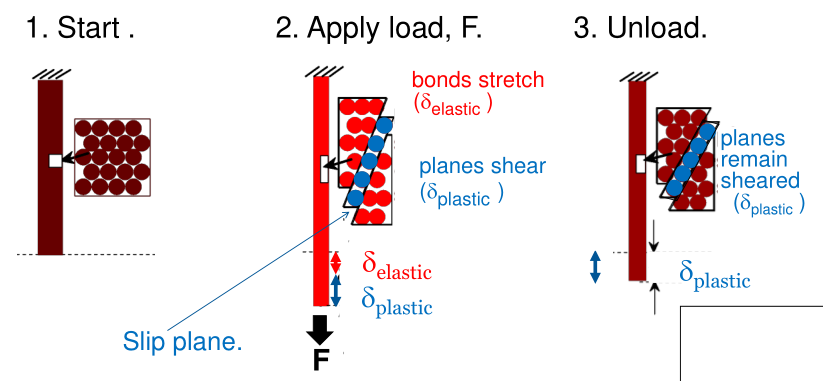
## Raising the Yield Stress of a Metal
There are 4 main ways to raise the yield stress of a metal:
- Make a solid-solution---by metal alloying or atomic addition
- Precipitate crystalline inclusions---by metal alloying or atomic additions and then heat treatment
- Work-harden --- by processing and/or cold-working
- Decrease the grain size --- by processing and/or heat-treatment
### Make a Solid-Solution
Adding an alloying element, B, to the host, A, forms a solid-solution as the ions or atoms of B
dissolve in A.
The impurity particles of B are a different size from the particles of A, distorting the metal
lattice.
The larger the difference in radii of the particles, the bigger the distortion.
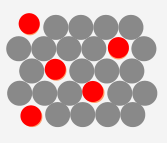
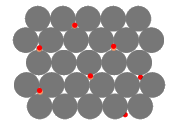
The particles of B tend to diffuse to dislocations and immobilise them.
This is why alloying increases the yield stress.
Impurity particles generate lattice strain in the structure too:
- Smaller particles introduce a compressive strain in the surrounding lattice
- Larger particles introduce a tensile strain in the surrounding lattice
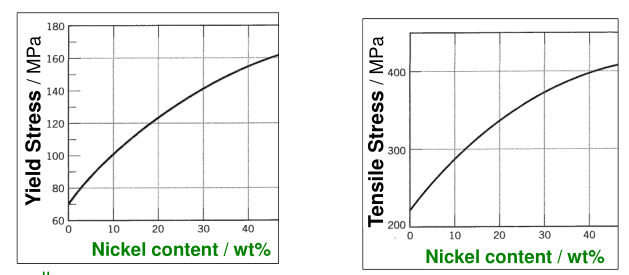
### Precipitating Crystalline Inclusions
When adding an element, B, to a host, A, exceeds the solubility, the result is the formation of a
solid-solution with a fixed ratio of B to A, but also precipitated crystals of a different ratio of
B to A.
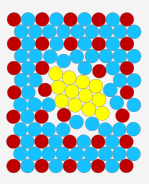
Crystalline inclusions are really difficult to shear, especially if they are small, numerous, and
have high Vickers' hardness.
This slows down dislocation movement, increasing yield stress.
### Work-Hardening and Cold Working
We can use room temperature deformation to increase the number of dislocations present in a metal.
As the % cold-work (%CW) is increased, the number of dislocations present also increases:
$$\% CW = \frac{A_0 - A_d}{A_0} \times 100\%$$
where $A_0$ is the initial cross sectional area and $A_d$ is the final cross sectional area.
A carefully prepared sample has a dislocation density, $\rho_d$ of around $10^3$ mm mm$3$,
whereas for a heavily deformed sample it is around $10^{10}$.
A high density of dislocations means they are more likely to get entangled with each other,
making it harder for dislocations to move.
Therefore as $\rho_d$ increases, yield stress does too.
### Decreasing the Grain Size
- Most metals are polycrystalline with many grains.
- Different grains will have a different crystal orientation.
- Grains impede dislocation motion
As you decrease grain size, you get more grain boundaries which basically creates more barriers
to prevent slip.
This is because a dislocation would have to change orientation across a grain boundary and "ionic
disorder in the grain boundary results in discontinuity of slip" (A.B Seddon, University of
Nottingham 2020) (I think that's repeating it but it said it on the slideshow sooo...).
So for any given metal, the fine grained is harder and has greater yield stress than the coarse
grained version of it.
#### Hall Petch Equation
$$\sigma_{yield} = \sigma_0 + k_yd^{-0.5}$$
where $d$ is the grain size and $\sigma_0$ and $k_y$ are material constants.
Therefore a plot of $\sigma_{yield}$ against $d^{-0.5}$ would results in a straight line.
## Heat Treatment of Metals
These processes are to change a material's mechanical properties, not change its shape.
### Phase Diagrams
Here is an example of a *two component phase diagram* with a familiar system:
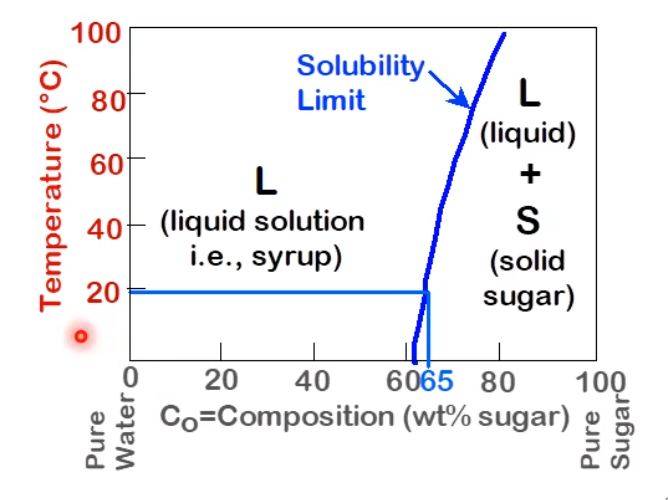
The component in this case are sugar and water, but not syrup.
A *phase* is a chemically and physically distinct species as we can have a change in phase that goes
from solid to solid.
The *solubility limit* is the maximum concentration for which only a solution occurs.
In the case of this system, thee limit increases with temperature.
Here is a generic phase diagram for a generic *A-B* system:
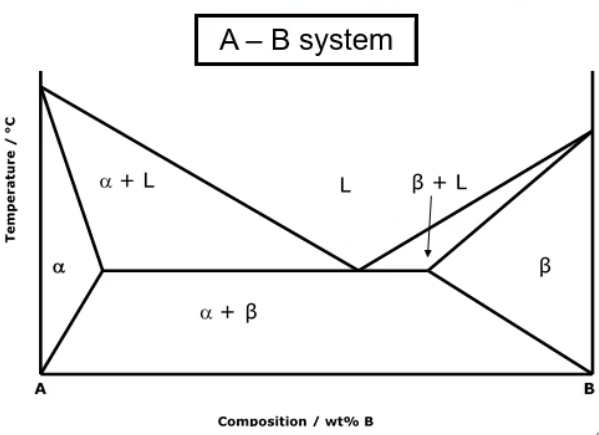
- L - liquid
- $\alpha$ --- a solid phase but still a solution. B can dissolve into A
- $\beta$ --- a solid phase but still a solution. A can dissolve into B
### Annealing
Annealing is a process by which a component is heated to remove the effects of cold work.
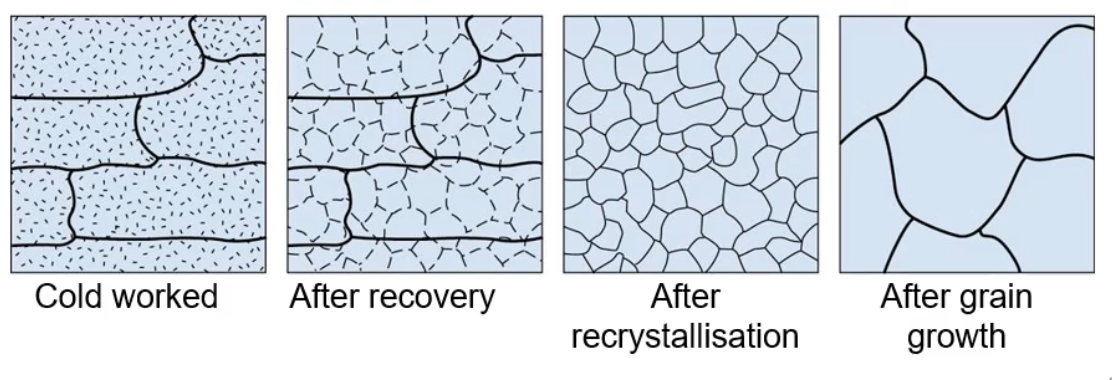
These are diffusional processes and only occur at high temperatures.
The driver for diffusion is the removal of high energy defects from the system.
# Diffusion
Diffusion is atomic or ionic movement down a concentration gradient.
## Solid State Diffusion
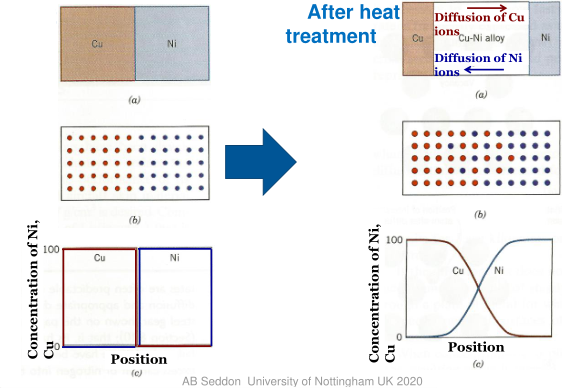
Solid state diffusion is the stepwise migration (*march*) of atoms or ions through a lattice, from
site to site.
In order for this to happen, there must an adjacent vacant site.
The diffusion particle must also have sufficient thermal energy to 'jump' to the new site.
### Vacancy Diffusion (Diffusion of Metal Ions)
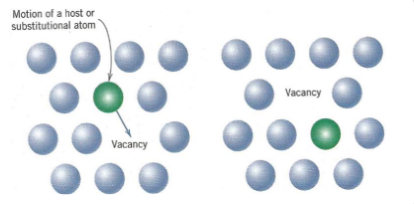
### Interstitial DIffusion (Diffusion of Small, Non-Metallic Particles)
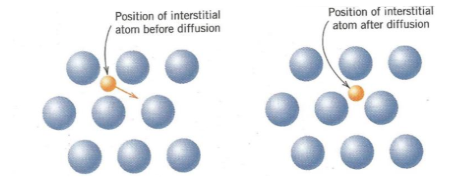
## The Math(s) of Diffusion
Diffusion is time dependent.
For steady state diffusion, Fick's 1st Law holds:
$$J = -D \frac{\mathrm{d}C}{\mathrm{d}x}$$
where $J$ is the *flux*, $\frac{\mathrm{d}C}{\mathrm dx}$ is the concentration gradient, and $D$ is
the constant of proportionality known as the *diffusion coefficient*.
$D$ is constant for a particular metal at a particular temperature.
The *flux*is the number of atoms or ions moving per second through a cross sectional area.
### Things that Affect the Speed of Diffusion
- size of the diffusion species --- smaller species results in faster diffusion
- temperature --- more thermal energy allows more particles to have enough energy to make the 'jump'
- host lattice
- simple cubic --- 52% occupancy of ions
- body centered cubic --- 68% occupancy of ions
- face centered cubic --- 74% occupancy of ions
Diffusion is faster in a BCC host than in an FCC host for iron ions in an iron host and also for
carbon atoms diffusing into an iron host.
However this is not always the case.
### Influence of Temperature on Diffusion (Arrhenius Equation)
You can apply the Arrhenius equation for all thermally activated diffusion:
$$D = D_0 \exp{\left( - \frac{Q}{RT} \right)}$$
where $D$ is the diffusion coefficient, $D_0$ is the frequency factor, $Q$ is the activation energy,
$R$ is the ideal gas constant (8.31 J k$^{-1}$ mol$^{-1}$).
You can find the diffusion distance, $x$, with the following equation:
$$x ~ \sqrt{Dt}$$
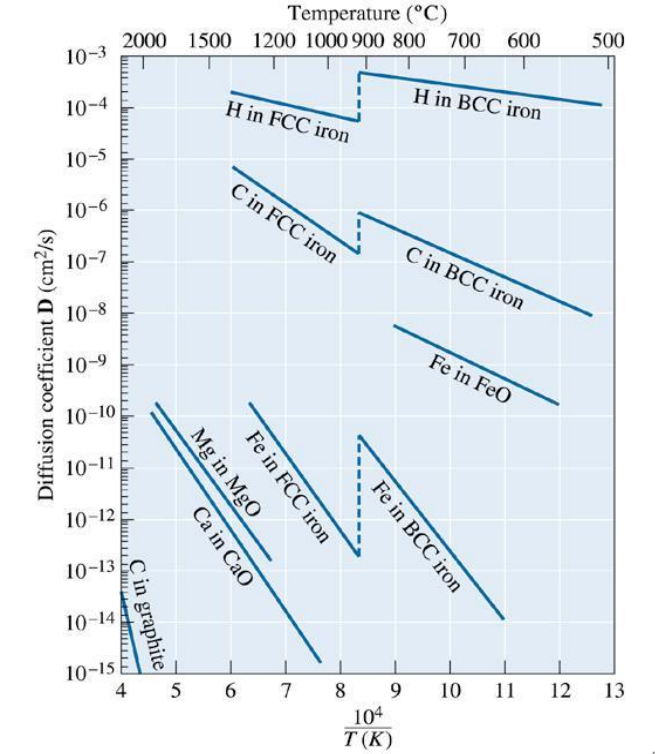
# Materials in Sustainable Transport
- Concerns over use of fossil fuels, climate change
- Const of energy
- Energy use in making and moving vehicles
- Rising energy prices mean cost of fuel is comparable to cost of car
- 1/4 of energy used in UK is to transport goods and people
- Legislation and voluntary targets set by EU to improve fuel efficiency
- In 2015 average CO2 emmisions as 130 g / km
- Engine powerhas gone up significantly from 2001 to 2018 (~30%) yet engine displracement has gone
down ~10% and CO2 emissions down ~18% while weight has gone up ~10%
## Is the car emissions reduction target significant?
Overall CO2 emissions in 2016 is 466 Megatonnes.
Does a reduction from 130 g / km to 95 g / km (a 35 g/km reduction) make a significant difference?
There are 33 million registered cars in the uk.
If they average around 8000 miles each (~13000 km) per year that's a ~15 Megatonne reduction,
or about 3% of the annual C02 emmissions, a significant reduction.
## Materials in Cars
- Most of the energy used by cars is during driving (71%)
- This means the mass of the vehicle has a great effect on its emmissions across a lifetime
- The body, suspension, drivetrain, and interior all contribute roughly a quarter to the mass of the
car
- However, the mass of cars are increasing
### Material Substitution
- The material will likely have performance requirements:
- It may need to be a physical size
- It may need to operate at certain temperatures
- It may need to bear a certain load
- The component mustalso be designed for convenient manufacturing, assembly, servicing, disposal,
remanufacturing and/or disassembly
#### Case Study --- 2012 Honda Accord
- Body --- opted to stay with steel --- aluminium intense and multi-material approaches were both
rejected due to higher costs and limitations in manufacturing and assembly.
Recyclability was also noted as an issue due to different grades of aluminium needing to be
separated at end of life.
- Doors and bonnets --- move to aluminium from steel --- more costly but the mass savings made this
option worth it
- Wiring --- aluminium to copper --- lower mass for same conductivity, copper is more expensive
(I think)
- Seats --- steel to composites or magnesium structural components --- very high weight savings
## Choosing a Material
# Glossary
- liquidus - for a system of more than one component, the liquidus is the lowest temperature at
which the whole system is all in the liquid state.
- solidus - for a system of more than one component, the solidus is the highest temperature at which
the whole system is still in the solid state